In a country
where engineering and manufacturing are no longer seen as innovative
Morris Material Handling are bringing excitement to a very traditional
industry. Loughborough based Morris with approximately 350 staff
and a market leading range of over head travelling cranes and hoists
are now distributing, installing and servicing product throughout
the world.
The flagship
projects Morris supply cranes to are massive by any standards. The
more recent ones include cranes to lift 400 tonnes and 200 tonnes
for transformer manufacturing, 3 cranes each lifting 130 tonnes
as part of the new Mubarak pumping station in Egypt, and a 70 metre
span crane for the aviation industry. Projects of this size require
considerable attention to detail, and high engineering values. This
same attention to detail can also be seen in the company's latest
electric chain hoist, the S3, the UK's leading electric chain hoist.
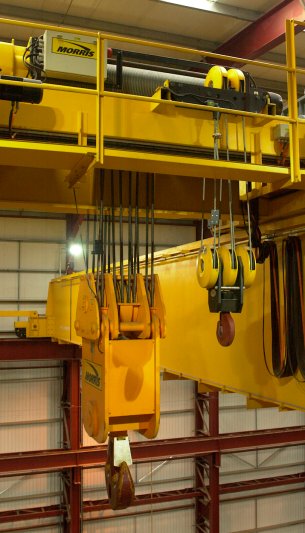
The increasing
sophistication in cranes and crane software is matched by increasing
sophistication in electric chain hoists. The Morris S3 range of
high performance electric chain hoists is one of the market leaders
in the new generation of high specification hoists. When developing
the S3 high engineering values and increased operator safety were
the key design criteria. The result was a competitively priced high
specification hoist, bristling with safety features, that also knows
its own operating history. From the data collected the owner can
tell how long the hoist has been operating and if it is being abused.
Changing health and safety legislation is increasingly making this
sort of knowledge important.
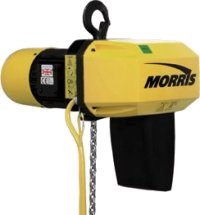 |
|
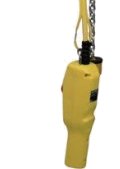 |
The
Morris Institute, a dedicated training facility is yet another
innovative idea. This full-service training organisation provides
on-site, regional and international training and safety instruction
in an interactive atmosphere, giving hands-on experience to
both operators and maintenance personnel. The courses include
'off the shelf' courses or purpose designed to the customer's
precise requirements. |
|
|
|
The Loughborough
factory has one of most modern hoist manufacturing facilities in
Europe, and the development of the site is continuing. Currently
the rest of the site is now being redeveloped to bring it into line
with 21st century manufacturing requirements. There is no doubt
that in what is normally considered as traditional manufacturing
Morris is an innovator.
|
|
Cranes
carrying the Morris name can be found in almost every industry,
be it power generation, manufacturing, water treatment, metals production,
or more recently waste to power plants. The breadth of industries
which Morris serves means that every crane is different. These differences
may be minor, such as the size of the building, or, every detail
of the application could be unique. Meeting this breadth of design
requirements in the past has not been easy, but with the development
of Cranesolve (Morris' unique crane design and specification software)
customers can see their crane designed in front of their eyes. This
flexibility offers the customer the opportunity to see and evaluate
different cranes before deciding on the best specification for his
needs.
In the UK,
customers buy complete cranes, but for export markets (where Morris
frequently supply through agents) most cranes are exported as kits.
The main components of the crane (the hoist, end carriages, the
electrical panels and control gear) are produced in the UK, and
the girder is produced locally to a Morris design. To support export
customers Kitsolve has been developed. Like Cranesolve, Kitsolve
designs the whole crane and then identifies the major components
of the kit for production in the UK, before producing the design
drawings for the non UK content.
However, bigger
export projects are designed in the UK, manufactured in the UK and
then exported to be commissioned by Morris staff on site. One of
these is the Mubarak Pumping Station in Egypt. This is one of the
largest pumping stations ever built, and Morris is supplying 5 cranes
to the project. Everything about the cranes is on a grand scale,
there are 3 cranes with capacities of 130 tonnes for lifting pumps
and the 2 smaller 30 tonne gate cranes each have a height of lift
of approximately 60 metres.
Typically cranes
have a useful life of 20-30 years, often more. When investing money
for this length of time crane owners need to know that they will
be able to get parts and service for the life of the crane. Morris,
through its material handling centres, network of independent distributors
and foreign agents supply parts for the installed base of Morris
equipment throughout the world. Among the innovative parts resources
is a swift order shop (SOS) dedicated to providing parts support.
"This is a unique facility. When a non stock part is needed urgently
for a breakdown we can make it, and frequently we find ourselves
doing so over night." According to Bernard Grantham Parts Manager
at Morris, as second innovative parts service is Allparts. Allparts
mission is to supply any part for any crane any time; this may be
standard off the shelf items or bespoke engineered parts manufactured
in the SOS shop. As was recently the case when the company produced
2 hoist drums. Each drum was approximately 4.5m long and 3.5m tall,
critical spares for a 500t crane used for steel making.
|