|
With
cranes having a typical useful life of 20-30 years, often more, maintenance
managers should recognise the value of crane maintenance. When investing
money for this length of time crane owners and operators need to be
aware of the common causes of crane misuse breakdown and inefficiency,
and adopt cost saving training and maintenance programmes that will
uphold their cranes efficiency. The effectiveness of equipment
used in manufacturing such as cranes has an influence on an organisations
entire operation from product quality to on time delivery. Industrial
managers who implement effective maintenance and training programmes
usually realise profound affects, gain increased control over the
performance of their organisation and consequently achieve real success.
According to
Morris Material Handling, the UKs leading crane and Hoist
Manufacturer, the common causes of crane misuse, breakdown and inefficiency
include ineffective operation by uninformed operators, plant neglect
and poor maintenance practices. By implementing successful scheduled
maintenance programmes, operator training and crane refurbishment
and upgrading programmes, the efficiency and reliability of cranes
can be significantly improved and immediate and long-term dividends
will be produced through the adoption of these preventative, value
enhancing and cost reducing courses of action. The programmes benefits
can be summarised as follows:
|
|
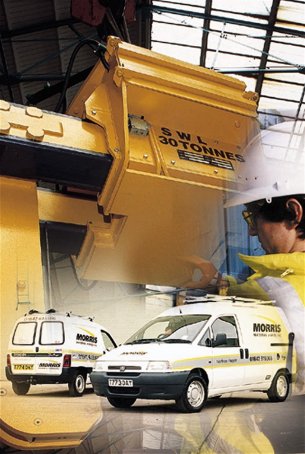 |
1.The
benefits of scheduled maintenance, operator and maintenance personnel
training
|
Scheduled
maintenance
The key to a successful maintenance programme is scheduling and
execution. It is commonly recognised that unscheduled repairs are
much more costly than scheduled repairs. Breakdowns can be costly,
particularly those that occur out of normal working hours and require
urgent repair. Downtime, out of hours service, and loss of production
can be major costs, and collateral damage, and damage to long lead
items should not be underestimated. The cost of breakdowns can in
many cases be double the cost of repairing the equipment prior to
failure. Therefore it is important to review, monitor and maintain
the condition of cranes on a regular basis, and employ preventative
rather than reactive maintenance.
Operator
training
To achieve optimum operating performance it is essential that there
is good co-ordination and co-operation between operations and maintenance
managers. Utilising operator training to ensure the crane is correctly
operated also helps to reduce running costs and generate income,
adding bottom line profits by improving the productivity and effectiveness
of the operator, reducing downtime and limiting damage.
|
|
Training
employees in Maintenance skills
Improving employees maintenance skills often plays a big part
in a successful maintenance programme. A quality preventative maintenance
programme requires highly motivated and skilled maintenance personnel.
The provision of precision maintenance training and the employment
of the right techniques and procedures for preventative/predictive
maintenance on specific equipment, is a highly valuable in developing
the essential skills and motivation of maintenance staff.
Benefits
in short: |
|
Reduced
production downtime |
|
Increased
efficiency and improved productivity |
|
Reduced
long term running costs |
|
The
risk of breakdown and costly production delays are minimised |
|
Extension
of component life cycle, eliminating the premature replacement
of machinery and equipment |
|
Compliance
with H&S rules and regulations is promoted improving
safety and quality conditions |
|
An
economical, cost effective use of maintenance workers |
|
|
2.
The benefits of Refurbishment and Modernisation
|
Through refurbishment
and modernisation an ageing crane can be rejuvenated close to a
new specification. Its performance and life span can also
be improved through the incorporation of new technology. Refurbishment
and modernisation can improve a cranes safety and ensure that
it complies with Health and Safety rules and regulations. These
alteration and modification activities can also enhance the reliability,
functionality and capacity of cranes and reduce maintenance costs.
Modern controls provide smoother operation, more precise load spotting
and reduced maintenance costs.
New operational
activities or demands often instigate the requirement for crane
refurbishment and upgrading. For example, when Aluminium producer
Alcan needed their pot room cranes refurbishing and updating they
called upon Morris engineers. By modernising and refurbishing eight
of their cranes used to lift containers of molten metal, through
the introduction of remote controls and motorised power slewing
processes, Morris reduced the number of staff involved in the operation
and increased safety and efficiency.
Outsourcing
Many companies have found that using outside contractors for equipment
maintenance and training is more effective than in-house provision.
There are numerous benefits of utilising a specialist external contractor,
not least the acquisition of expert advice and service. Morris Material
Handling is one such company that can act in this capacity, the
key benefits of selecting Morris as a service provider include:
- Specialist
advice and service from a the UKs leading manufacturer of
cranes and hoists.
- Local support
from a network of independent distributors across the UK.
- Tailored
solutions that meet exact operational requirements and corporate
objectives and ensure maximum crane utilisation and total value
for money.
|
|
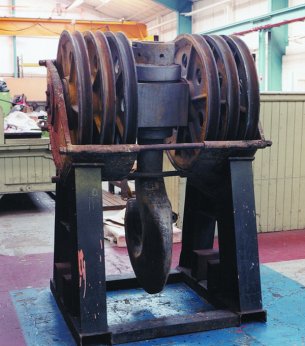
Before and after
pictures of Alcan's crane bottom blocks
refurbished by Morris
|
Morris Material
Handling supply many industry leaders with crane maintenance programmes.
Two such companies that have recently selected Morris specialist
crane service and inspection contracts are steel producer Corus
and vehicle component supplier Dana Spicer. The company offers an
unrivalled package within the industry combining leading edge design
and the latest manufacturing techniques, complimented by a full
installation and support service. Through its material handling
centres, network of independent distributors and foreign agents
Morris provide parts and service for all cranes, irrespective of
manufacturer wordwide. The companys service division is supported
by Morris Allparts and Morris Swift Order Shop dedicated to
the supply of engineered and assembled Morris and Non-Morris parts
24 hours a day.
Morris
dedicated training facility, the Morris Institute, has run numerous
courses in equipment maintenance, operation and efficiency and in
health and safety for many of the UKs leading businesses.
British Nuclear Fuels recently chose the Morris Training institute
to provide their maintenance engineers with crane maintenance tuition,
following other comprehensive Morris training programmes presented
to the company. Other institutions who have benefited from Morris
comprehensive courses include English, Welsh and Scottish Railways,
UK Coal, The Royal Naval Lifeboat institute and the UKs governments
Health and Safety Executive.
|
|
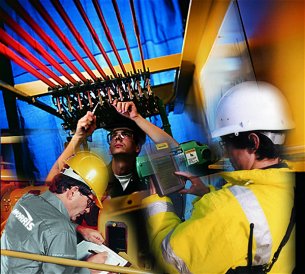
In the drive
to bring health and safety issues to the attention of industry and
business, the Institute has worked closely with other industry bodies
such as the Heath & Safety Executive, the Institute of Occupational
Safety & Health, the Road Transport Industry Training Board
and the Engineering Construction Industry Training Board. This full-service
training organisation provides on-site, regional and international
training and safety instruction in an interactive atmosphere, giving
hands-on experience to both operators and maintenance personnel.
The courses include off the shelf courses or purpose
designed to the customers precise requirements.
|
|
|