The Maintenance Services Division of leading lifting services
provider, Morris Material Handling, is actively promoting a new
and invaluable managed service that is being rolled out across
all industry sectors here in the UK.
Branded 'AIMS' (Asset Inspection Management System), the service
has been created to help customers radically reduce risk
associated with potential load failures. Developed by Morris' inhouse
team of IT specialists working in conjunction with
maintenance services, AIMS uses the latest in hand-held
technology as a means of accurately identifying all lifting
equipment, be it overhead cranes or below the hook across all
site premises.
Comments Pat Campbell, operations director, maintenance services
at Morris Material Handling: "Having successfully trialled the
new AIMS system with a number of our key customers, we have taken
the decision to actively promote its use amongst both our entire
customer base and prospects. AIMS is a highly-effective tool and
one that serves to ensure that accident risk associated with
defective items of lifting equipment is kept to an absolute
minimum. This achievement is primarily delivered through the
efficiency of the reporting that the system delivers, and its
subsequent ability to schedule the management process required to
rectify items of non-compliance.
"Furthermore, AIMS serves to reduce the potential of incidence
associated with lifting equipment failure through the speed of
identification of potentially problematic or defective items,
thereby providing complete peace of mind for the customer. This
is ultimately achieved as a result of the speed with which
current reportable data is supplied following an inspection
visit. In essence, under the AIMS system, the prime focus is
always on prevention rather than cure." he added.
HOW IT WORKS
Deployed by Morris Material Handling's team of LEEA trained
technical support engineers, the service initially involves the
compilation of an equipment register or asset database that
covers all equipment to be inspected. Once collected, this
information is stored on Morris' own central IT system database
that is Microsoft driven.
With the register in place, which then forms the working base
from which all future inspections are carried out, the condition
of each item of lifting or below the hook equipment listed is
entered onto palm-top technology. This current reported
information is then up-loaded to the equipment register database,
delivering an extremely efficient method for data transfer.
And it is here that AIMS really comes into its own, as the
database provides a very efficient method of identifying both
defective items and any required corrective actions that are
necessary. At this point, AIMS has the capacity to detail
specific reports that immediately identify items that require
repair or which cannot be found, and those that should be taken
out of service following the inspection visit. Such is the
sophistication of reporting that AIMS can deliver, it is also
possible to output copies of Certificates Of Thorough Examination
for compliance with the LOLER98 regulations, as and when
required. However the system in itself offers the ability of
providing a paperless reporting system.
COLOUR CODING
In order to further reduce the incidence of accident risk from
potential load failure, during an AIMS inspection visit every
single item of lifting equipment is colour coded for the relevant
inspection period, thereby making it immediately identifiable to
personnel that it is safe to use. Should any item be located
displaying a colour other than that of the current inspection
period it should be removed from use until inspected again.
As Pat Campbell states: "Perhaps the single biggest benefit that
AIMS delivers is the speed with which information can be relayed
through to a client following an inspection visit. Under normal
circumstances, we aim to forward full and comprehensive
inspection results typically within five working of any visit to
our clients' premises nationally."
So in summation, using AIMS, Morris Material Handling is able to
offer customers a fully managed service when it comes to reducing
the risk associated with potential load failures. For as well as
identifying defective items, Morris also has the capabilities to
oversee full repair and maintenance work, shifting the onus away
from the customer from having to do so themselves.
Anyone interested in exploring the benefits that AIMS can deliver
should contact Morris Material Handling's Maintenance Services
Division.
|
|
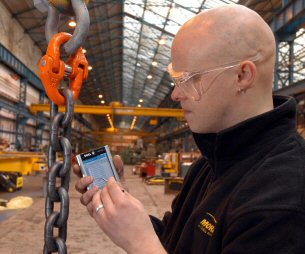
|